AI Computer Vision: Reducing Downtime in Industrial Furnaces
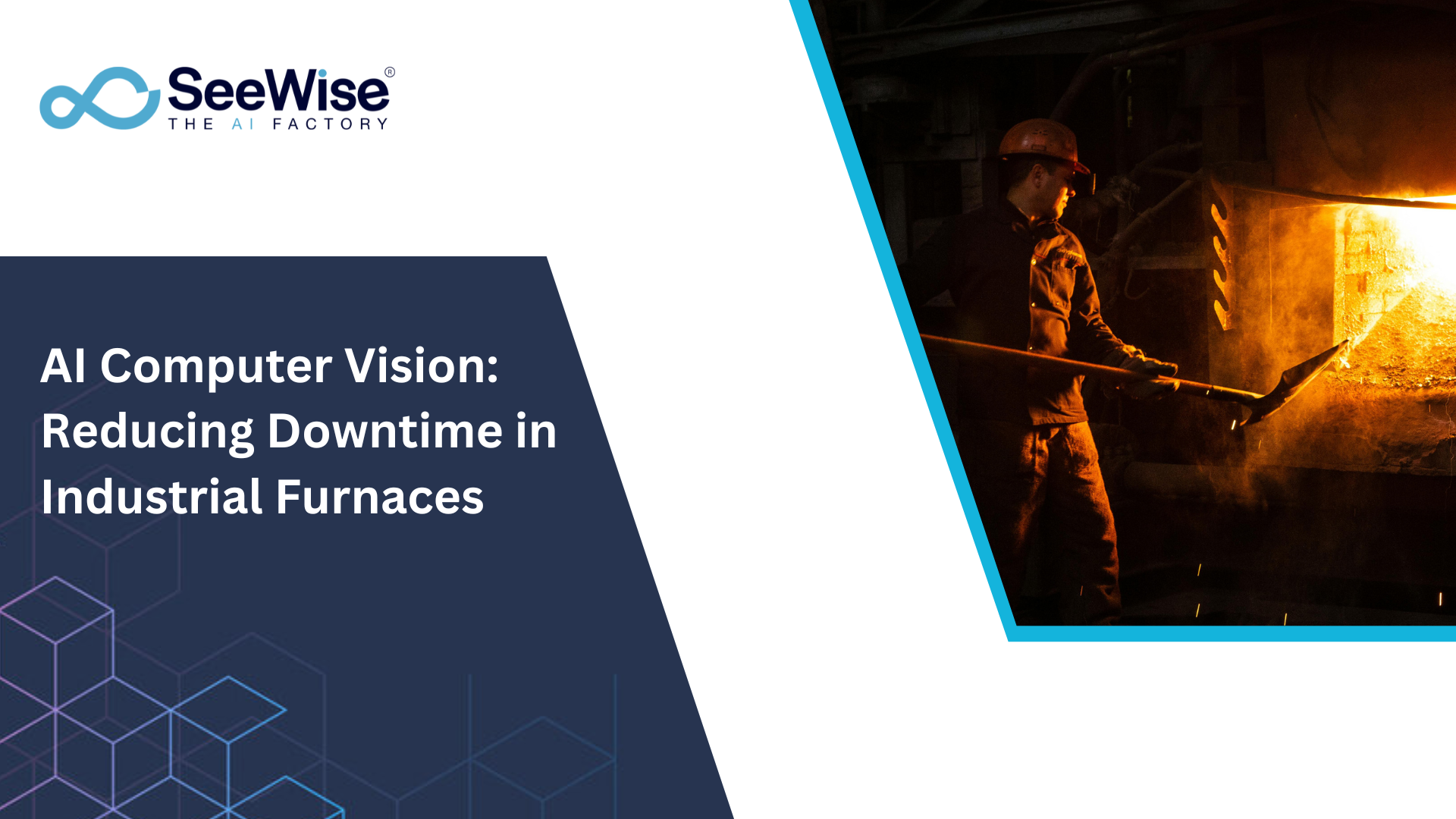
Did you know that unplanned downtime in industrial furnaces can cost companies up to $22,000 per minute? Imagine the financial impact of just one hour of unexpected downtime—over a million dollars lost!
But here's the exciting part: AI-driven computer vision technology is revolutionizing the way industries manage their furnaces, significantly reducing these costly interruptions. By leveraging advanced vision analysis, companies can predict and prevent issues before they escalate, ensuring smoother operations and substantial savings. This technology is a key component of Industry 5.0, where advanced AI and IoT (AIOT) solutions integrate seamlessly to enhance industrial processes.
In this blog, we’ll explore how AI computer vision is transforming industrial furnace maintenance, the technology behind it, and the incredible benefits it brings to the manufacturing sector.
Introduction
Industrial furnaces are critical components in numerous manufacturing processes, from metal smelting to glass production. These high-temperature environments are essential for achieving the desired properties of materials, but they also pose significant challenges in terms of maintenance, efficiency, and industry safety. Unplanned downtime in industrial furnaces can lead to substantial financial losses, production delays, and even safety hazards. However, the advent of AI-driven computer vision technology is providing new solutions to mitigate these issues, offering predictive maintenance and real-time monitoring capabilities that were previously unattainable.
Historical Context of Furnace Maintenance
Traditionally, furnace maintenance has been a reactive process. Operators relied on scheduled inspections and manual checks to identify potential issues. This approach, while somewhat effective, often led to unforeseen breakdowns and extended periods of inactivity. Early warning signs, such as minor temperature fluctuations or changes in material appearance, were easily overlooked, leading to larger, more costly problems down the line. With the introduction of basic automation and control systems in the late 20th century, some improvements were made. However, these systems were limited in their ability to provide detailed, real-time analysis. It wasn't until the integration of AI and computer vision, hallmark technologies of Industry 5.0, that a true transformation began to take place.
The Role of AI and Computer Vision
AI computer vision technology uses advanced algorithms to analyze visual data captured by cameras installed in and around industrial furnaces. This technology offers several key advantages:
- Real-Time Monitoring: AI systems continuously monitor the furnace environment, detecting anomalies in real-time. This constant vigilance ensures that even the slightest deviations from normal operating conditions are identified immediately, enhancing industry safety.
- Predictive Maintenance: By analyzing patterns and trends in the visual data, AI can predict potential failures before they occur. For instance,changes in the color or texture of furnace linings can indicate wear and tear that might lead to a breakdown if not addressed promptly.
- Improved Safety: Automated monitoring reduces the need for human intervention in hazardous environments. This not only enhances worker safety but also ensures that inspections are more thorough and consistent.
- Data-Driven Insights:AI systems can process vast amounts of data,providing operators with actionable insights. These insights help in optimizing furnace operations, reducing energy consumption, and extending the lifespan of equipment.
Reducing Downtime: A Detailed Analysis
- Early Fault Detection: One of the most significant benefits of AI computer vision is its ability to detect early signs of faults. For example, a slight deformation in the furnace structure or an unusual pattern in the flame can be indicative of underlying issues. Traditional methods might miss these subtle clues, but AI algorithms are designed to recognize them instantly.Early detection allows maintenance teams to address problems before they escalate, thereby preventing costly downtime.
- Optimizing Maintenance Schedules: AI-driven insights enable more precise maintenance scheduling. Instead of relying on predetermined intervals, maintenance can be performed based on the actual condition of the furnace. This approach, known as predictive maintenance, ensures that resources are used more efficiently. It also means that maintenance activities are less likely to disrupt production, as they can be scheduled during periods of low demand.
- Enhancing Process Control:In addition to maintenance, AI computer vision improves overall process control. By continuously monitoring the furnace environment, AI systems can adjust operating parameters in real-time to optimize performance. This includes regulating temperature, adjusting fuel feed rates, and controlling air flow. These adjustments help maintain optimal conditions, reducing the likelihood of issues that could lead to downtime.
The Future of AI in Industrial Furnaces
The integration of AI and computer vision in industrial furnaces is still in its early stages, but the potential is enormous. Future advancements could include more sophisticated algorithms capable of diagnosing a wider range of issues, as well as enhanced integration with other smart factory technologies. For instance, AI could work in tandem with IoT devices to provide a holistic view of the entire production process, a concept central to AIOT. This would enable even more precise control and optimization, further reducing downtime and improving overall efficiency.
Conclusion
Reducing downtime in industrial furnaces is crucial for maintaining production efficiency, minimizing costs, and ensuring safety. AI computer vision offers a powerful tool for achieving these goals, providing real-time monitoring, predictive maintenance, and enhanced process control. As the technology continues to evolve, its impact on the manufacturing industry will only grow, paving the way for smarter, more efficient operations. By understanding the significance of AI computer vision in this context, readers can appreciate the transformative potential of this technology and its role in shaping the future of industrial manufacturing, a vision aligned with the principles of Industry 5.0.