Supercharging Foundry Melting Units with AI
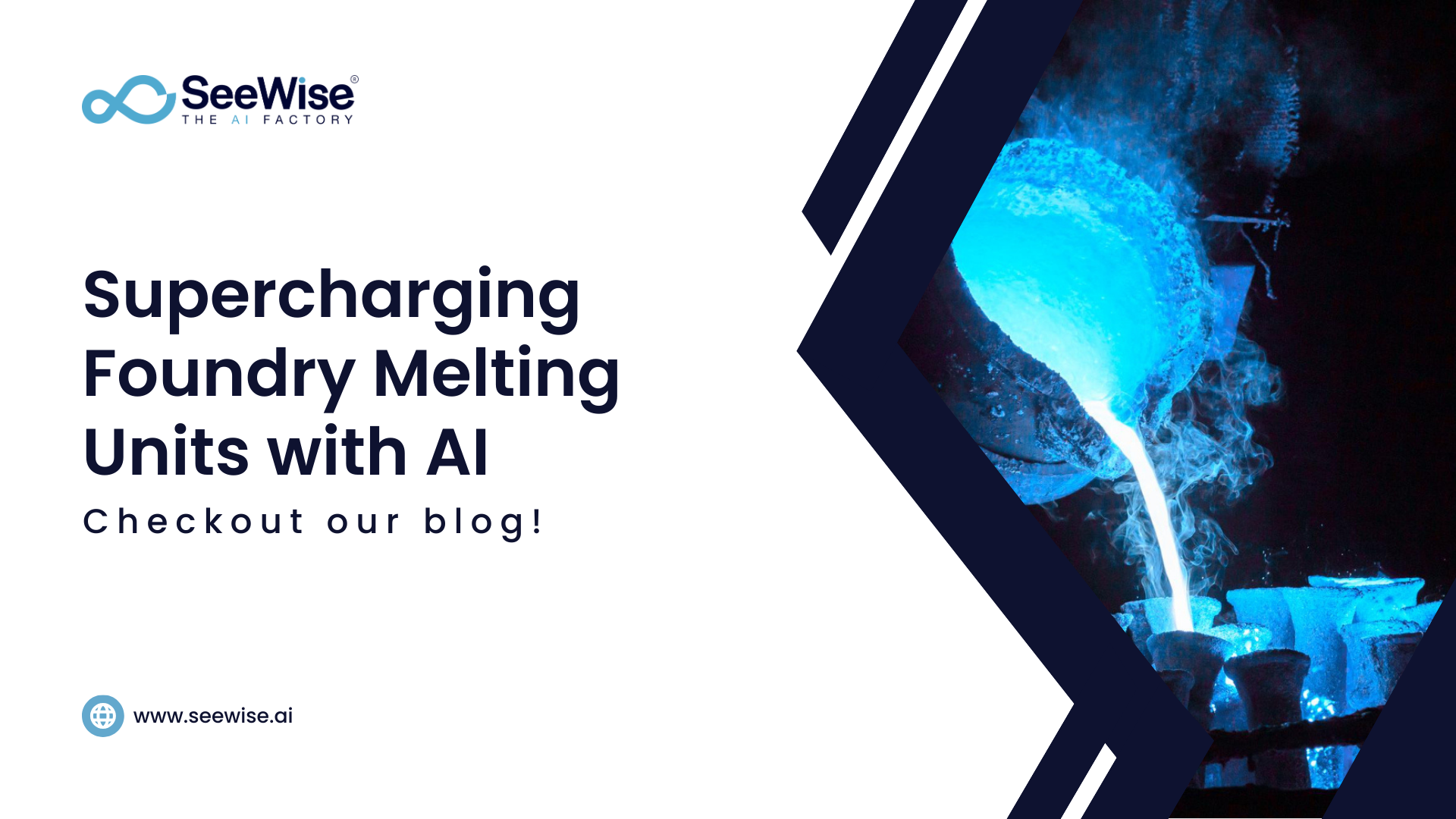
Supercharging Foundry Melting Units with AI: Boost Efficiency and Precision Like Never Before
Melting units are the beating heart of any metal manufacturing operation, but let’s face it—keeping them running smoothly is no easy feat. From high energy bills to inconsistent melting precision and safety concerns, it’s a daily battle. Traditional melting setups demand constant attention, often dragging your team into inefficiency, long downtimes, and wasting resources. Worse yet, this slows down production and drives up your carbon footprint—taking a toll on your sustainability goals.
Enter AI: A Game Changer for Melting Units
Artificial Intelligence (AI) is shaking up industries, and the foundry world is catching on. As we move into Industry 5.0, AI-driven tools are addressing energy efficiency, precision, and safety issues in ways we never thought possible. From AI Smart Cameras to Large Vision Models, these tech marvels are transforming how we manage melting units. Think real-time data insights, predictive maintenance, and smart systems that can adjust on the fly. Welcome to the future of metal manufacturing!
How AI Tools Are Redefining Melting Operations
In this blog, we’ll take you through how cutting-edge AI solutions like AI Smart Cameras and Large Vision Models are changing the game in foundries. These innovations are driving more precise operations, saving energy, cutting down on waste, and boosting safety across the board. In short, by embedding AI into your foundry’s melting process, you’re stepping into the future—where human know-how teams up with machine precision.
1. Industry 5.0: The Sweet Spot Where Humans & AI Collaborate
From Industry 4.0 to Industry 5.0
Industry 4.0 was all about automation, IoT, and data. But Industry 5.0 takes it up a notch by focusing on human-machine collaboration. Instead of machines replacing us, they now work with us, fine-tuning operations and making decisions faster and smarter. For foundries, this evolution opens the door to customized, flexible production processes, powered by AI.
Precision & Sustainability: Why It Matters
In melting units, a tiny temperature slip can ruin an entire batch. With AI tools, you’ll maintain perfect precision, monitor energy consumption like never before, and cut waste. This means not only better operations but also a smaller carbon footprint—a win for both your business and the planet.
2. AI in Action: Optimizing Your Foundry’s Melting Unit
The shift to AI-driven control in foundries is already making waves. AI systems monitor every aspect of energy usage, temperature, and material consistency in real-time. They tweak things automatically—meaning less waste, less downtime, and longer equipment life. Even better, AI can predict issues before they happen, like catching a rise in temperature that might lead to a breakdown.
3. AI Smart Cameras: The Eyes Watching Your Melting Units
Forget regular surveillance cameras. AI Smart Cameras are on another level. Equipped with machine learning, they don’t just record—they analyze what’s happening in real-time, offering insights that can save your operation from costly mistakes. Real-Time Monitoring & Quality Control AI Smart Cameras are constantly scanning for changes in temperature, material quality, and equipment status. Spot a problem? They’ll alert your team instantly, stopping potential disasters before they happen. This instant feedback loop ensures your foundry is always performing at its best. Preventing Failures Before They Strike The real magic happens with predictive insights. AI Smart Cameras don’t just catch issues—they predict them. Based on historical data, they can warn you when equipment is likely to fail, giving you time to schedule maintenance before you’re forced into expensive repairs or downtimes.
4. AI-Powered Insights: Seeing What Humans Can’t
When it comes to melting metal, Large Vision Models take precision to the next level. These AI tools dive deep into the melting process, analyzing microscopic details like material composition and subtle temperature shifts. The result? Improved uniformity, less waste, and better energy efficiency.
A Real-World Success Story
Consider a European foundry that was dealing with fluctuating temperatures and uneven product quality. After adopting Large Vision Models, they cut energy usage by 15%, reduced material waste by 10%, and saw a massive improvement in product consistency. This technology doesn’t just provide insights—it delivers actionable solutions that make a real difference.
5. AI and Humans: A Powerful Partnership
Industry 5.0 in Practice
Industry 5.0 is all about collaboration—where AI tools support human operators rather than replace them. In a foundry, this is key. While AI can handle the data-heavy aspects like real-time monitoring and predictive analytics, humans are still essential for decision-making and tackling unexpected situations. Augmenting Decision-Making & Boosting Safety AI doesn’t take the human element out of the equation—it enhances it. Operators can make smarter decisions, faster, because they have AI providing them with real-time data. And let’s not forget about safety. By monitoring the entire process continuously, AI can alert operators to potential hazards, keeping both your team and your operations safe
The Future Is Here, and It’s AI-Powered
The integration of AI Smart Cameras and Large Vision Models is transforming foundry melting units. We’re talking better precision, higher energy efficiency, and enhanced safety. As Industry 5.0 evolves, the collaboration between human expertise and AI will only grow more vital.
Ready to future-proof your foundry? The early adopters are already seeing big results. Don’t get left behind—take the leap into AI-driven solutions today.
At Seewise, we offer tailored AI solutions designed specifically for foundries. Our tools will help you transition smoothly into Industry 5.0, unlocking new levels of efficiency and precision.
Visit Seewise.ai and start transforming your melting operations today!